Pneumatische Zylindersensoren - Wie sie funktionieren
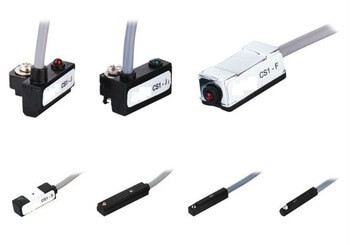
Abbildung 1: Verschiedene pneumatische Zylinder-Näherungssensoren
Sensoren sind unerlässlich, um Positionsrückmeldungen an Steuerungssysteme in automatisierten Maschinen und Geräten zu liefern. In pneumatischen Zylindern werden Sensoren verwendet, um die lineare Position des Kolbens zu erfassen, was für Anwendungen, die eine präzise Positionsrückmeldung erfordern, entscheidend ist. Die am häufigsten verwendeten Sensoren für pneumatische Zylinder sind magnetische Näherungssensoren, die das Magnetfeld eines im Zylinderkolben eingebetteten Magneten erkennen. Diese Sensoren sind am Gehäuse des pneumatischen Zylinders montiert und zeigen "EIN" oder "AUS" an, je nach ihrer Nähe zum Magneten. Abhängig von der spezifischen Anwendung können verschiedene Technologien magnetischer Näherungssensoren eingesetzt werden, um Leistung, Platz und Zuverlässigkeit zu optimieren. Abbildung 1 zeigt Beispiele für verschiedene Näherungssensoren für pneumatische Zylinder.
Reed-Sensoren sind die gängigste Art von Pneumatikzylinder-Sensoren. Sie werden seit Jahren eingesetzt und sind eine bewährte Technologie. Die beiden Hauptgründe, die für einen Reed-Sensor im Vergleich zu anderen Sensoren sprechen, sind die Lebensdauer und Schock-/Vibrationsprobleme. Reedsensoren haben in der Regel eine Lebensdauer von mehr als 10 Millionen Jahren, und in der Regel ist der Reedsensor nicht der erste, der ausfällt, wenn er starken Stößen oder Vibrationen ausgesetzt ist. Aus diesen Gründen sind Reed-Sensoren nach wie vor der beliebteste Sensor für Pneumatikzylinder.
Sehen Sie sich unsere Online-Auswahl an Pneumatikzylindern und Sensoren an!
Inhaltsübersicht
- Warum einen Sensor für einen Pneumatikzylinder verwenden?
- Montage des Pneumatikzylinder-Sensors
- Optionen für magnetische Näherungssensoren
- Wie wählen Sie zwischen den Sensoren aus?
- Vergleiche von Pneumatikzylinder-Sensoren
- Positionssensoren online kaufen
Warum einen Sensor für einen Pneumatikzylinder verwenden?
Lineare Positionssensoren für Pneumatikzylinder werden verwendet, um die lineare Position des Kolbens während des Betriebs zu erfassen. Pneumatikzylinder werden in der Regel mit einem Magneten hergestellt, der bereits im Inneren des Kolbens angebracht ist, so dass auf Wunsch magnetische Näherungssensoren verwendet werden können. Je nachdem, wo der Sensor angebracht ist, kann er das Ausfahren, das Einfahren oder einzelne Positionen entlang des Zylinderkörpers erkennen. Es können auch mehrere Sensoren an einem Pneumatikzylinder angebracht werden, um mehrere Positionsrückmeldungen zu erhalten. Pneumatikzylinder mit Positionssensoren bieten zusätzliche Sicherheit und Rückmeldung, um die Kolbenposition für wichtige Anwendungen zu gewährleisten.
Montage des Pneumatikzylinder-Sensors
Die beiden gebräuchlichsten Arten von Pneumatikzylindern sind Profilzylinder, wie ISO 15552, oder runde Zylinder, wie ISO 6432. Je nach Karosserietyp gibt es unterschiedliche Befestigungsmethoden. Auch die Montagemethoden können sich je nach Sensortyp ändern. Daher ist es wichtig, den Typ des Zylindergehäuses und den Sensortyp zu kennen.
Profil-Zylinder
Profilzylinder haben eine rechteckige Form und verfügen über zwei einfache Methoden zur Befestigung von Sensoren am Zylinderkörper. Bei Pneumatikzylindern, die der ISO-Norm 15552 entsprechen, sind entlang des Gehäuses Nuten vorhanden, in die ein Sensor eingesetzt werden kann (siehe Abbildung 2). Der Sensor (1) wird dann mit einer Stellschraube (2) mit einem Schraubendreher (3) befestigt. Andere Profilzylinder haben Zugstangen, die an allen vier Ecken über die gesamte Länge des Zylinderkörpers verlaufen. Die Sensoren können auf der Zugstange montiert und an die entsprechende Position entlang des Zylinders geschoben werden.
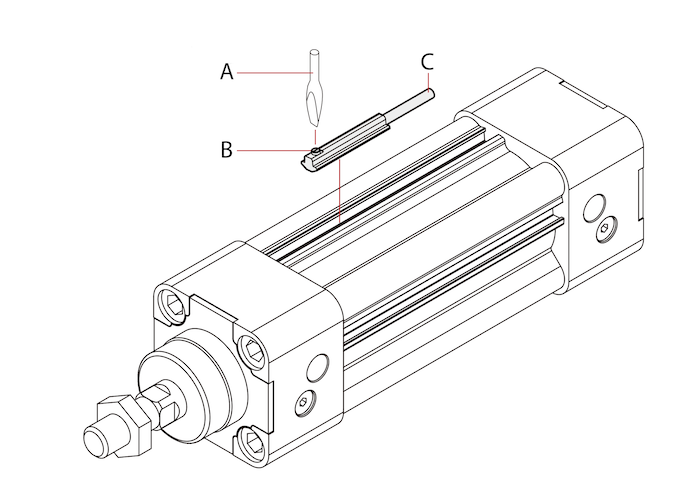
Abbildung 2: Pneumatikzylinder nach ISO 15552 mit einem Sensor (C), der über eine Stellschraube (B) mit einem Schraubendreher (A) befestigt wird
Runde Zylinder
Runde Zylinder sind in der Regel kleiner, wie z. B. ISO 6432, aber Sensoren können trotzdem daran befestigt werden, indem ein kreisförmiges Band um das Gehäuse des Zylinders gelegt wird. Das Band muss entsprechend dem Durchmesser des Zylinders festgelegt werden. Nach der Montage können der Sensor und das Band über die Länge des Zylinders gleiten und dann befestigt werden. In Abbildung 3 ist ein pneumatischer Zylinder nach ISO 6432 mit einem darauf montierten Sensor zu sehen.
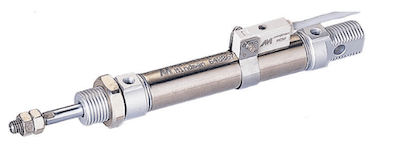
Abbildung 3: Pneumatikzylinder nach ISO 6432 mit montiertem Sensor
Optionen für magnetische Näherungssensoren
Alle Sensoren, die bei Pneumatikzylindern zur Rückmeldung der linearen Position des Kolbens verwendet werden, nutzen ein Magnetfeld. Daher haben alle Pneumatikzylinder in der Regel bereits einen Magneten, der sich im Inneren des Kolbens befindet. Dennoch ist es wichtig, diese Konstruktionsspezifikation für Ihren Pneumatikzylinder zu überprüfen, wenn eine lineare Positionsrückmeldung erforderlich ist.
Reed-Schalter
Ein Reed-Sensor ist ein magnetischer Näherungssensor, der eingeschaltet wird, wenn ein axial ausgerichtetes Magnetfeld an ihn angelegt wird. Die Magnetpole eines axial ausgerichteten Magneten liegen in der axialen Ebene nebeneinander. Wenn sich der axial ausgerichtete Magnet dem Zungensensor nähert, wird ein Magnetfeld parallel zum Zungenschalter erzeugt. Ein Reedschalter besteht aus einem Paar ferromagnetischer Metallzungen, die in einem versiegelten Glasrohr eingeschlossen sind. Ohne das Vorhandensein eines Magnetfeldes (Abbildung 4 oben) werden die Metallzungen getrennt, und der Sensor wird ausgeschaltet. Wenn der Zylinderkolben den Schalter passiert und ein Magnetfeld anlegt, das stark genug ist, um die Zungen zusammenzuziehen (mittleres Bild, Abbildung 4), wird der Sensor eingeschaltet (unteres Bild, Abbildung 4).
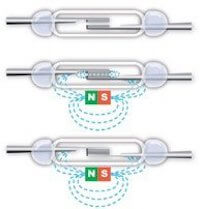
Abbildung 4: Reedschalter-Betrieb
Im Vergleich zu anderen Sensoroptionen sind Reed-Schalter kostengünstig und können mit Wechsel- oder Gleichspannungen betrieben werden. Außerdem haben Reed-Sensoren einen geringen Stromverbrauch und eignen sich daher für Anwendungen, die einen hohen Stromverbrauch erfordern. Aufgrund der mechanischen Beschaffenheit der schaltenden Reedkontakte haben Reedschaltersensoren ihre Grenzen. Erstens haben die Schaltkontakte eine endliche Anzahl von Schaltzyklen und müssen über die Lebensdauer der Maschine hinweg gewartet werden. Außerdem sind Reed-Sensoren nicht für Anwendungen geeignet, die starken Vibrationen oder Stößen ausgesetzt sind. Starke Erschütterungen und Vibrationen können dazu führen, dass die Reedkontakte klappern und dadurch ungenaue Signale abgeben. Die Schalteigenschaften eines Reed-Schalters können auch zu unbeabsichtigten Doppelschaltungen führen. Doppeltes Schalten bedeutet, dass der Sensorausgang zweimal "EIN" und "AUS" schaltet, während der Zylindermagnet den Reedschalter einmal passiert. Die falsche Doppelschaltung des Sensorausgangs ist auf die ungleichmäßige Stärke des Kraftfelds eines Magneten zurückzuführen. Die Stärke eines Magnetfeldes ist an jedem Pol des Magneten am stärksten und in der Mitte zwischen den Polen am schwächsten. Wenn der Kolbenmagnet nicht stark genug ist, kann er dazu führen, dass der Schaltausgang doppelt schaltet, wenn er den Sensor passiert. Schließlich sind Reedschalter im Vergleich zu Halbleitersensoren relativ langsam in der Aktivierung, was sie für Anwendungen, die schnelle Reaktionszeiten erfordern, ungeeignet macht. Reedschalter-Sensoren für Pneumatikzylinder sind jedoch weit verbreitet, da sie im Vergleich zu anderen Sensoren relativ preiswert sind, keine Standby-Leistung benötigen, sowohl mit Gleich- als auch mit Wechselstrom funktionieren und eine bewährte, bekannte Lösung darstellen.
Hall-Effekt-Sensor
Ein Hall-Effekt-Sensor ist ein magnetischer Näherungssensor, der eingeschaltet wird, wenn ein radial ausgerichtetes Magnetfeld an ihn angelegt wird. Ein radial ausgerichteter Magnet erzeugt ein Magnetfeld, das senkrecht zum Magnetfeld des Halleffektsensors steht, wie in Abbildung 5 zu sehen ist. Im Gegensatz zu Reed-Schaltern sind Hall-Effekt-Sensoren Festkörpergeräte und bestehen aus anderen Komponenten. Reedschalter sind auf bewegliche mechanische Kontakte angewiesen, um einen Sensorausgang zu liefern. Solid-State-Geräte liefern einen Sensorausgang, indem sie elektrische Schaltungen ohne bewegliche Komponenten verwenden. Ein Hall-Effekt-Sensor besteht aus einem Halbleiter, durch den ein kontinuierlicher Strom fließt, wie im oberen Bild in Abbildung 5 zu sehen ist. Wenn ein Magnetfeld radial (2) an den Stromfluss (1) angelegt wird, wie im unteren Bild in Abbildung 5 zu sehen, trennen sich die geladenen Elektronen je nach Polarität auf gegenüberliegenden Seiten des Halbleiters. Die Trennung der geladenen Elektronen induziert eine Spannung in der Halleffektschaltung (4). Sobald die Ausgangsspannung an der Schaltung größer als die Schaltschwelle ist, wird der Sensorausgang eingeschaltet, wie in Abbildung 5 zu sehen ist.
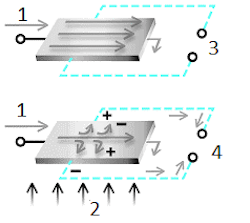
Abbildung 5: Betrieb eines Hall-Effekt-Sensors: Stromfluss (1), Magnetfeld (2), Spannung = 0 (3 & 4)
Im Gegensatz zu Reed-Schalter-Sensoren enthalten Halleffekt-Sensoren keine beweglichen Komponenten und benötigen eine kleinere Montagefläche. Die Halbleiterkonstruktion erhöht die Lebensdauer des Sensors durch den verschleißfreien Betrieb und macht ihn unempfindlich gegen Stöße und Vibrationen. Da die Trägheit mechanischer Komponenten nicht überwunden werden muss, eignen sich Hall-Effekt-Sensoren auch für zeitkritische Anwendungen, die schnelles Schalten erfordern. Ähnlich wie bei Reed-Sensoren ist die Ausrichtung des Magneten wichtig für den ordnungsgemäßen Betrieb. Außerdem haben Hall-Effekt-Sensoren eine geringe Empfindlichkeit. Je nach Durchmesser und Dicke des Zylinderkörpers kann es sein, dass der Schaltausgang nicht richtig aktiviert wird. Ähnlich wie bei Reed-Schaltern sind auch hier aufgrund der geringen Empfindlichkeit der Sensoren doppelte Schaltpunkte möglich.
Anisotroper magnetoresistiver Sensor
Ein anisotroper magnetoresistiver Sensor (AMR) ist ein magnetischer Näherungssensor, der eingeschaltet wird, wenn ein radiales oder axiales Magnetfeld an ihn angelegt wird. Eine AMR-Schaltung besteht aus einer Wheatstone-Brückenschaltung (Abbildung 6) zur Widerstandsmessung. Der Widerstand eines AMR-Sensors nimmt mit der Stärke des Magnetfelds ab, was zu einem größeren Spannungsgradienten im AMR-Kreis führt. Sobald die Spannung am Schaltkreis größer ist als die Schaltschwelle (Abbildung 6 Nummer 3), wird der Sensorausgang eingeschaltet (siehe Abbildung 6 Nummer 4).
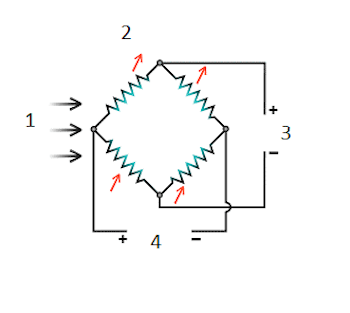
Abbildung 6: Betrieb des AMR-Sensors: Magnetfeld (1), angelegtes Magnetfeld (2), Vorspannung (3) und Spannung = 0 (4)
Ähnlich wie Hall-Effekt-Sensoren arbeiten AMR-Sensoren schnell, sind verschleißfrei und unempfindlich gegenüber Stößen und Vibrationen. Der Vorteil von AMR-Sensoren ist, dass sie weniger empfindlich sind als Hall-Sensoren und gut auf Änderungen der Magnetfeldstärke reagieren. Dies führt zu einer verbesserten Kolbenerkennung über größere Entfernungen, da es schwächere Magnetfelder erkennen kann. Die Möglichkeit von doppelten Schaltpunkten wird durch die höhere Empfindlichkeit ausgeschlossen. Außerdem erkennen die Sensoren axial und radial magnetisierte Magnete. AMR-Sensoren sind kompakter als Reed-Sensoren und kostengünstiger. Ein Nachteil von AMR-Sensoren ist, dass sie in der Regel kontinuierlich Strom verbrauchen. Für Anwendungen, die einen geringen Stromverbrauch erfordern, kann ein Reed-Sensor die bessere Wahl sein.
Riesiger magnetoresistiver Sensor
Ein riesiger magnetoresistiver Sensor (GMR) ist ein magnetischer Näherungssensor, der eingeschaltet wird, wenn ein radiales oder axiales Magnetfeld an ihn angelegt wird. Ein GMR-Sensor besteht aus verschiedenen Schichten mit abwechselnd magnetischen und nichtmagnetischen leitenden Schichten, wie in Abbildung 7 Nummern 2 und 3 zu sehen ist. Ähnlich wie bei einem AMR-Sensor ändern sich die Widerstandseigenschaften des Schaltkreises, wenn ein Magnetfeld an den Sensor angelegt wird, wodurch ein höherer Spannungsgradient über den Schaltkreis entsteht, wenn das Magnetfeld zunimmt. Bei Vorhandensein eines Magnetfeldes (Abbildung 7 Nummer 1) sinkt beispielsweise der Widerstand des Stromkreises, so dass Strom fließen kann (Abbildung 7 Nummer 4) und die Spannung im Stromkreis steigt. Sobald die Spannung über dem Stromkreis größer als die Schaltschwelle ist, wird der Sensorausgang eingeschaltet (ON).
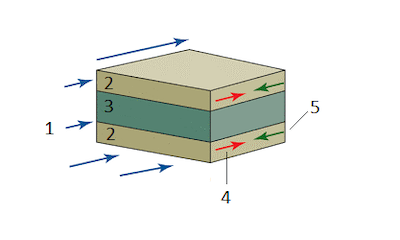
Abbildung 7: Funktionsweise des GMR-Sensors: Angelegtes externes Magnetfeld (1), ferromagnetische Schicht (2), leitende nichtmagnetische Schicht (3), niedriger Widerstand bei angelegtem Magnetfeld (4) und hoher Widerstand ohne externes Magnetfeld (5)
GMR-Sensoren bieten ähnliche Vorteile wie AMR-Sensoren, reagieren jedoch noch empfindlicher auf das Vorhandensein eines Magnetfeldes. Die hohe Empfindlichkeit ermöglicht auch einen sehr kompakten Sensor, der für kleinere und kürzere Zylinder geeignet ist. Die hohe Empfindlichkeit ist zwar ein Vorteil für Anwendungen, die eine unmittelbare Rückmeldung des Sensors erfordern, kann aber zu unbeabsichtigten Ausgangssignalen führen, wenn sie durch umgebende Magnetfelder gestört werden. So können z. B. Umgebungen mit hoher Leistung in der Nähe (Wechselstrommotoren oder Wechselstromeinspeisung) das Sensorsignal stören und unbeabsichtigte Fehler verursachen.
Wie wählen Sie zwischen den Sensoren aus?
Für die meisten Anwendungen wird in der Regel ein Zungensensor gewählt. Sie sind eine bewährte Technologie und verfügen über eine ausreichend lange Lebensdauer und Vibrationsbeständigkeit für gängige Anwendungen. Weitere Kriterien, die bei speziellen Anwendungen zu berücksichtigen sind, sind:
- Umwelt: Ist der Zylinder starken Vibrationen oder Stößen ausgesetzt? Wenn dies der Fall ist, arbeitet ein Halbleitersensor zuverlässig und ohne Ausgangsflattern. Übliche Halbleitersensoren sind Hall-Effekt-, AMR- und GMR-Sensoren. Wird der Sensor in einer geschlossenen, sauberen Umgebung eingesetzt oder benötigt er ein hochgradig geschütztes Gehäuse (z. B. IP67)? Auch die Temperatur sollte berücksichtigt werden.
- Umschaltgeschwindigkeit: Wie wichtig ist die Ausgangsschaltgeschwindigkeit für Ihre Anwendung? Halbleitersensoren bieten eine schnellere Schaltzeit. Übliche Halbleitersensoren sind Hall-Effekt-, AMR- und GMR-Sensoren.
-
Ausgangstyp: Welche Art von Ausgangssignal wird von der Steuerung benötigt? Für Halbleitergeräte sind PNP- und NPN-Ausgangssignale verfügbar.
- PNP: Ein PNP-Ausgang bietet einen Pfad zur Versorgung des Ausgangs mit positiver Spannung. Dies wird auch als "Beschaffung von Sensoren" bezeichnet. PNP ist in Nordamerika und Europa häufiger anzutreffen.
- NPN: Ein NPN-Ausgang bietet einen Pfad für die Versorgung zur Masse. Dies wird allgemein auch als "sinkender Sensor" bezeichnet. NPN wird in Asien als beliebter angesehen.
- Merkmale des Schaltsignals: Wie hoch ist die Schaltleistung und der Strombedarf des Steuersystems? Der gewählte Sensor sollte für einen ordnungsgemäßen Betrieb kompatibel sein.
- Befestigung Welche Befestigungsmöglichkeiten gibt es für die einzelnen Zylindertypen? Je nachdem, ob es sich um einen Profilzylinder mit Nuten oder Zugstangen oder um einen Rundzylinder handelt, ändern sich die Befestigungsarten.
- Magnet-Ausrichtung: Reedschalter und Hall-Effekt-Sensoren erfordern eine korrekte Ausrichtung des angelegten Magnetfelds, um ordnungsgemäß zu funktionieren. Daher muss der Sensor in der richtigen Ausrichtung zum Kolben montiert werden.
- Stromkreisschutz: Bei Bedarf können die Sensoren mit Schutzschaltungen wie Kurzschluss-, Verpolungs- und Überspannungsschutz ausgestattet werden.
- Verkabelung: Die Verdrahtung der Stromversorgung zum Sensor unterscheidet sich je nachdem, ob es sich bei dem Sensor um einen Halbleitersensor (z. B. AMR, GMR, Halleffekt) oder einen Reed-Sensor handelt. Häufig ist für jeden Sensor eine LED zur Anzeige der korrekten Verdrahtung vorhanden. Wenn zum Beispiel die Polarität der Stromversorgung eines Reed-Schalters vertauscht wird, leuchtet die LED am Sensor nicht. Reedschalter-Sensoren haben in der Regel eine 2-Draht-Konfiguration, während Solid-State-Sensoren 3-Draht haben. Zusätzlich zu einem Plus- und einem Minuskabel wird ein drittes Kabel für den Anschluss an die Last verwendet. Die korrekte Verdrahtung des Lastkabels sollte immer überprüft werden, bevor der Strom eingeschaltet wird, da eine falsche Verdrahtung den Sensor dauerhaft beschädigen kann.
Vergleiche von Pneumatikzylinder-Sensoren
Reed-Schalter | Hall-Effekt | AMR | GMR | |
Größe | Groß | Klein | Mittel | Klein |
Konstruktion: | Mechanisch | Fester Zustand | Fester Zustand | Fester Zustand |
Erforderliche Magnetstärke | Mittel | Hoch | Niedrig | Niedrig |
Empfindlichkeit: | Mittel | Niedrig | Hoch | Hoch |
Temperaturstabilität | Mittel | Niedrig | Mittel | Hoch |
Stromverbrauch | Zero | Niedrig | Hoch | Niedrig |
Störfestigkeit | Hoch | Niedrig | Hoch | Hoch |
Schaltgeschwindigkeit | Niedrig | Hoch | Hoch | Hoch |
Mechanische Robustheit | Niedrig | Mittel | Hoch | Hoch |
Elektrische Robustheit | Niedrig | Niedrig | Hoch | Hoch |
Doppelte Schaltpunkte | Ja | Möglicherweise | Nein | Nein |
Lesen Sie unseren Artikel über Pneumatikzylinder, um mehr über die Funktionsweise und die Arten von Pneumatikzylindern zu erfahren.