Kompressor-Entlastungsventile
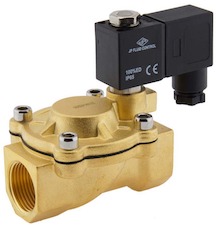
Abbildung 1: Luftkompressor-Entlastungsventil
Ein Luftkompressor-Entlastungsventil lässt eingeschlossene Luft aus dem Kompressionstank und der Entladungsleitung des Kompressors ab, wenn der Motor stoppt, was einen einfacheren Neustart ermöglicht. Es gibt zwei Haupttypen von Luftkompressor-Entlastungsventilen: elektrische und mechanische. Das Entfernen der Luft ist entscheidend, damit der Kompressormotor mit minimalem Aufwand wieder starten kann. Wenn die Luft nicht entfernt wird, erzeugt die durch die eingeschlossene Luft in der Kompressionskammer und der Tankentladungsleitung erzeugte Last ein hohes Anfangsdrehmoment, das der Motor möglicherweise nur schwer überwinden kann. Abbildung 1 zeigt ein Beispiel für ein elektrisches Luftkompressor-Entlastungsventil.
Inhaltsverzeichnis
- Wie funktioniert ein Luftkompressor-Entlastungsventil?
- Arten von Luftkompressor-Entlastungsventilen
- Mechanische vs. Solenoid-Entlastungsventile
- Auswahlkriterien für elektrisches Entlastungsventil
- Installation und Verkabelung eines Solenoid-Kompressor-Entlastungsventils
- Häufige Probleme lösen
- FAQ
Sehen Sie sich unsere Online-Auswahl an Kompressor-Entlastungsventilen an!
Wie funktioniert ein Luftkompressor-Entlastungsventil?
Die Funktion eines Entlastungsventils in einem Luftkompressor besteht darin, die verbleibende Luft aus der Kompressionskammer und den entsprechenden Leitungen freizusetzen, wenn der Motor ausgeschaltet wird. Der Betrieb eines Luftkompressors wird im Diagramm in Abbildung 2 erläutert, um zu verstehen, wie dieses Ventil funktioniert.
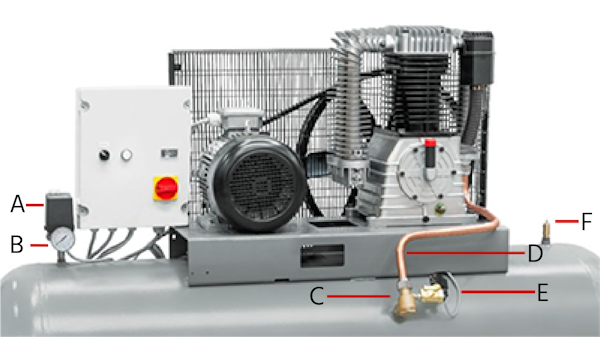
Abbildung 2: Luftkompressor-Komponenten, Druckschalter (A), Manometer (B), Rückschlagventil (C), Behälter-Austrittsleitung (D), Entlastungsventil (E) und Sicherheitsventil (F).
Ein Luftkompressor funktioniert nach folgenden Prinzipien:
- Vor dem Erreichen des Tanks durchläuft die komprimierte Luft einen Druckschalter (Abbildung 2 mit A gekennzeichnet), der den Druck zwischen den festgelegten maximalen und minimalen Grenzwerten bewertet.
- Während der Kompressor arbeitet, sammelt der Tank komprimierte Luft, bis der Druck sein voreingestelltes Maximum erreicht.
- Bei Erreichen seines maximalen voreingestellten Werts übt der Tankdruck eine Kraft auf einen internen Kolben des Druckschalters aus, bewegt ihn nach oben, trennt seine Kontakte und schaltet den Motor ab.
- Die Luft in der Kompressionskammer und der Behälter-Austrittsleitung (Abbildung 2 mit D gekennzeichnet) wird sofort durch das Entlastungsventil (Abbildung 2 mit E gekennzeichnet) in die Atmosphäre abgelassen.
- Diese Aktion schließt das Rückschlagventil (Abbildung 2 mit C gekennzeichnet) und verhindert, dass die Luft im Tank entweicht.
- Sobald der Tankdruck sein Minimum erreicht, kommen die Kontakte des Druckschalters (Abbildung 2 mit B gekennzeichnet) wieder zusammen, und der Motor startet erneut.
Arten von Luftkompressor-Entlastungsventilen
Obwohl sich Kompressor-Entlastungsventile je nach Kompressortyp und Hersteller unterscheiden, gibt es zwei Hauptarten: mechanisch und elektrisch.
Mechanische Entlastungsventile
Dieser Ventiltyp funktioniert entsprechend dem Druckunterschied. Es öffnet sich, wenn der Druck einen vorbestimmten Wert erreicht. Abbildung 3 zeigt ein Diagramm eines mechanischen Kompressor-Entlastungsventils.
Abbildung 3, Schritt A, zeigt Luft aus dem Kompressor, die durch den Einlass (1) in das mechanische Entlastungsventil gelangt, durch die Entlastungsventilkammer (2) zum Rückschlagventil (5). Die vom Luftdruck ausgeübte Kraft öffnet das Rückschlagventil und ermöglicht es der komprimierten Luft, durch den Auslass (6) zum Speichertank zu gelangen und auch zur Membrankammer (3) durch den Durchgang (4). Während der Tank mit komprimierter Luft gefüllt wird, steigt der Druck, bis er sein maximales Limit erreicht.
In Schritt B hebt die Membran (7) an und lässt Luft in die obere Kammer (8) des Kolbens (9) gelangen. Die in diese Kammer eintretende Luft drückt den Kolben nach unten, was es der in der Entlastungsventilkammer eingeschlossenen Luft ermöglicht, durch den Auslass (10) in die Atmosphäre abgelassen zu werden. Aufgrund des Druckabfalls schließt sich das Rückschlagventil automatisch.
Abbildung 3, Schritt C, zeigt, dass wenn sich das Rückschlagventil schließt, die Luft, die zur oberen Membran des Ventils gelangt, abnimmt, die Schubkraft gering ist und die Membran sich erneut schließt. Dies führt dazu, dass die in dem Hauptkolben eingeschlossene Luft durch die Gouverneursentlüftung (11) an der Spitze des Luftkompressor-Entlastungsventils (12) freigesetzt wird.
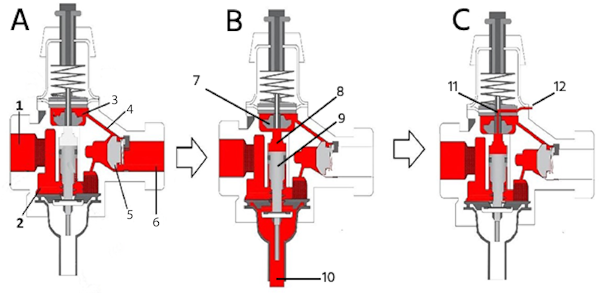
Abbildung 3: Diagramm des mechanischen Entlastungsventils: Einlass (1), Entlastungsventilkammer (2), Membrankammer (3), Durchgang (4), Rückschlagventil (5), Auslass (6), Membran (7), obere Kammer (8), Kolben (9), Auslass (10), Gouverneursentlüftung (11) und Luftkompressor-Entlastungsventil (12).
Elektrische Entlastungsventile
Ein Magnetspulenventil ist ein elektrisch betriebenes Gerät, das die Menge an Luft steuert, die durch eine Leitung strömt. Es schaltet, gibt frei oder dosiert den Durchfluss gemäß den Systemanforderungen. Schwerere Kompressoren (ab 5 kW) arbeiten oft mit einem Stern-Delta-System, um den Anlaufstrom des Motors zu reduzieren (im Vergleich zu einem Direktstart). Dieser Motor startet mit der Sternverbindung und wechselt dann von einem Stern zu einem Delta-Kreis. Während des Starts wird die Kompressorluft in den ersten Zyklen zu einem freien Auslass entlastet (anstatt zum Tank), um das erforderliche Drehmoment des Motors zu reduzieren. Ein Magnetspulenventil wird als Entlastungsventil verwendet.
Es gibt drei Arten von Magnetspulenventilen: direkt, halb-direkt und indirekt wirkend.
- Die Funktion des direkt wirkenden Ventils hängt nur von einem elektromagnetischen Feld ab, das in der Magnetspule erzeugt wird, um das Ventil zu schließen oder zu öffnen.
- Das indirekte Ventil hängt vom Druckunterschied im System ab.
- Das halb-direkt wirkende Ventil kombiniert die Funktionen eines direkt und indirekt wirkenden Ventils.
Zusätzlich bestimmt die Schaltfunktion eines Magnetspulenventils die Anschlüsse (2-, 3-, 4-Wege) und die Position des Ventils, wenn es nicht mit Energie versorgt wird (geöffnet oder geschlossen). Lesen Sie unseren technischen Artikel über Magnetspulenventile für weitere Informationen.
Das 2/2-Wege-Pilotventil ist das am häufigsten verwendete Magnetspulenventil für ein elektrisches Entlastungsventil für Luftkompressoren. Einer der Gründe dafür ist, dass dieser Ventiltyp für größere Luftströme von schweren Luftkompressoren im Vergleich zu direkt wirkenden Ventilen geeignet ist. Es ist auch der Ventiltyp mit dem geringsten Energieverbrauch. Dieser Ventiltyp wird auch als servounterstütztes Magnetspulenventil bezeichnet. Seine Funktion hängt vom Verhalten der Magnetspule und dem Druckunterschied im System ab (mindestens 0,5 bar sind für den Betrieb erforderlich). Im Allgemeinen hat das Ventil zwei Anschlüsse, einen für den Einlass und den anderen für die Luftabgabe, wie in Abbildung 4 zu sehen.
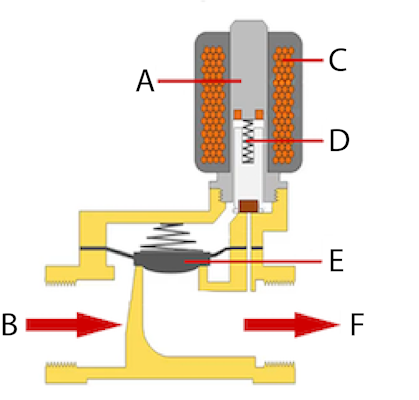
Abbildung 4: Ein indirektes Luftkompressor-Entlastungsventil: Anker (A), Einlassanschluss (B), Spule (C), Feder und Kolben (D), Membran (E) und Auslassanschluss (F).
Teile des Kompressor-Entlastungsventils
- Anker (A): Der metallische Zylinder, auf dem die Spule gewickelt ist
- Einlassanschluss (B): Die Luft gelangt durch diesen Anschluss in das Magnetspulenventil.
- Spule (C): Eine zylindrische, hohle Spule aus emailliertem Kupferdraht. Diese Spule speichert Energie in einem Magnetfeld durch Induktion.
- Feder und Kolben (D): Wenn in der Spule kein Magnetfeld vorhanden ist, hält die Feder den Kolben in einer bestimmten Position, normalerweise offen oder geschlossen. Die Feder gibt dem durch ein Magnetfeld auf den Kolben ausgeübten Druck nach.
- Membran (E): Schließmembran, die verhindert oder ermöglicht, dass Luft in die Atmosphäre abgelassen wird.
- Auslassanschluss (F): Dieser Anschluss gibt die Luft in die Atmosphäre ab.
In einem indirekten Magnetspulenventil gelangt die Luft über den Einlassanschluss (Abbildung 4 mit E gekennzeichnet) in den Bereich oberhalb der Membran durch eine Steueröffnung und verlässt diesen Bereich über die Pilotöffnung des Magnetspulenventils, die anfangs geschlossen ist, wie in Abbildung 5 (linke Seite) zu sehen.
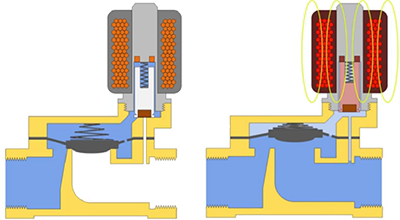
Abbildung 5: Diagramm eines normalerweise geschlossenen indirekten Ventils: nicht mit Energie versorgt (links) und mit Energie versorgt (rechts)
Wenn der Tank seinen maximalen Druck erreicht, wird die Magnetspule mit Energie versorgt, und der Magnetspulenventilkolben bewegt sich nach oben, öffnet die Pilotöffnung. Mit dieser offenen Leitung beginnt der Druck der Luft, die sich im Bereich oberhalb der Membran befindet, abzunehmen, bis ihr Wert niedriger ist als der Druck, der von der Luft über der Membran ausgeübt wird. Sobald diese Membran nach oben bewegt wird, gelangt die Einlassluft zum Auslass, wie in Abbildung 5 rechts zu sehen. Wenn der Tankdruck sein Mindestlimit erreicht, stoppt der elektrische Strom der Magnetspule, und die Pilotöffnung schließt sofort. Der Luftdruck in der oberen Kammer der Membran wird wiederhergestellt, und die Membran kehrt in ihre Ausgangsposition zurück, wodurch verhindert wird, dass Luft vom Einlass zum Auslass gelangt.
Ein normalerweise geschlossenes indirektes Ventil ist am häufigsten; es ist mit Energie versorgt (geöffnet) während des Sternschaltkreises und geschlossen während des Deltakreis-Anschlusses. Luftkompressoren mit dem Stern-Delta-Kreis verwenden jedoch auch ein normalerweise offenes Ventil. In diesem Fall erreicht der Tankdruck sein maximales Limit, der Druckschalter trennt seine Kontakte, der Motor stoppt, und das Magnetspulenventil öffnet sich (nicht mit Energie versorgt), um die Luft in die Atmosphäre abzulassen. Sobald der Tankdruck das Mindestdrucklimit erreicht, verbinden sich die Kontakte des Druckschalters, der Motor startet, und das Magnetspulenventil schließt sich (mit Energie versorgt), nachdem der Anschluss von Stern zu Delta gewechselt hat, wie in Abbildung 6.
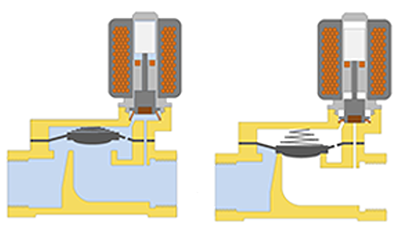
Abbildung 6: Diagramm eines normalerweise offenen indirekten Ventils: nicht mit Energie versorgt (links) und mit Energie versorgt (rechts).
Mechanische vs. Magnetspulen-Entlastungsventile
Mechanisch | Elektrisch | |
Einstellung | Kann manuell eingestellt werden | Wird am Druckschalter oder Timer eingestellt |
Timer | Kann nicht mit einem Timer betrieben werden | Kann mit einem Timer betrieben werden |
Position | Kann in jeder Position installiert werden | Sollte aufrecht oder mit maximaler Abweichung von 90° installiert werden |
Verstopfungen | Nicht empfindlich gegen Schmutz | Empfindlicher gegen Schmutz als ein mechanisches Ventil |
Anwendung | Ein mechanisches Entlastungsventil wird häufig in kleineren Kompressoren (weniger als 5 kW) verwendet | In schwereren Kompressoren (Drehstrommotor) wird typischerweise ein indirektes Magnetspulenventil als Entlastungsventil verwendet. |
Auswahlkriterien für elektrisches Entlastungsventil
Neben der Eignung des Ventils für die Arbeit mit Luft sollten bei der Auswahl eines Magnetspulenventils, das als Luftkompressor-Entlastungsventil verwendet werden soll, folgende Punkte berücksichtigt werden:
- Kapazität (Kv-Wert): Der Kv-Wert bestimmt den Luftdurchfluss durch das Magnetspulenventil. Die Kenntnis des erforderlichen Kv-Werts stellt sicher, dass das richtige Ventil mit der erforderlichen Kapazität ausgewählt wird. Berechnen Sie Kv- oder Cv-Werte mit unserem Ventilgrößenrechner.
- Maximaler Betriebsdruck: Das Magnetspulenventil muss in der Lage sein, den maximalen Arbeitsdruck des Kompressors zu bewältigen.
- Elektrische Steuerung: Ermitteln Sie, ob die Spannung des Ventils am Installationsort verfügbar ist. Überprüfen Sie, ob das System während der Luftablassperiode mit Strom versorgt wird oder ob ein integrierter Timer im Ventil verwendet wird, um die Öffnungszeit anzupassen. Überprüfen Sie außerdem, ob das System ein normalerweise offenes oder geschlossenes Ventil erfordert.
- Anschlusstyp und -größe: Stellen Sie sicher, dass die Gewinde der Rohre mit dem Einlassgewindetyp und der -größe des Magnetspulenventils übereinstimmen. Wenn die erforderliche Anschlussgröße des Magnetspulenventils nicht verfügbar ist, kann ein Fitting verwendet werden.
- Material des Magnetspulenventils: Für das Ventilgehäuse ist die Verwendung von Messing als Gehäusematerial und einer FKM (Viton)-Dichtung eine gute Wahl, da sie eine gute Hitze- und Chemikalienbeständigkeit aufweisen.
- IP-Klassifizierung: Magnetspulenventile, die in Luftkompressorsystemen verwendet werden, sollten eine IP65-Bewertung haben, um eine effektive Abdichtung gegen äußere Einflüsse sicherzustellen.
Installation eines Entlastungsventils an einem Luftkompressor
Die Installation und Verkabelung eines Magnetspulenkompressor-Entlastungsventils in ein Luftkompressorsystem umfasst mehrere wichtige Schritte.
- Zuerst die Sicherheit: Stellen Sie vor Beginn sicher, dass die Stromversorgung des Luftkompressors ausgeschaltet ist, um elektrische Gefahren zu vermeiden. Tragen Sie auch geeignete Sicherheitsausrüstung.
- Identifizieren des Magnetspulen-Entlastungsventils: Wenn ein Entlastungsventil ausgetauscht wird, sollte das alte Ventil zwei oder mehr Drähte für den elektrischen Anschluss haben. Es ist normalerweise in der Nähe des Druckschalters des Luftkompressors installiert. Es könnte in der Nähe des Rückschlagventils an der Behälter-Austrittsleitung angebracht sein.
- Das alte Ventil abklemmen:
- Elektrische Verbindungen: Trennen Sie vorsichtig die elektrischen Drähte, die mit der Magnetspule verbunden sind. Es ist ratsam, ein Foto zu machen oder die Drahtverbindungen für die Installation des neuen Ventils zu notieren.
- Das alte Ventil entfernen: Sobald alle Verbindungen getrennt sind, entfernen Sie das alte Magnetspulen-Entlastungsventil von seiner Halterung. Dies kann das Abschrauben aus einem Gewindeanschluss oder das Entfernen von Klammern oder Halterungen, die es an Ort und Stelle halten, umfassen.
- Das neue Ventil installieren:
- Platzieren Sie das neue Magnetspulen-Entlastungsventil an der richtigen Stelle. Stellen Sie sicher, dass es korrekt eingedreht ist, um ein Quetschen zu vermeiden.
- Installieren Sie zuerst den Ventilkörper. Verwenden Sie ein geeignetes Werkzeug, um das Magnetspulenventil festzuziehen, und ein weiteres, um die Systemrohre zu halten.
- Positionieren Sie den Ventilkörper so, dass die Spule nach oben zeigt oder maximal 90 Grad abweicht, um das Risiko von externen Einflüssen auf den Magnetspulenventilkolben zu minimieren.
- Installieren Sie die Spule. Platzieren Sie sie auf dem Ventilkörper, mit ihrer Dichtung und Mutter darüber, und ziehen Sie sie fest. Eine Richtlinie für das Drehmoment sind 5 Nm, aber das Handbuch des Magnetspulenventils sollte eine Festlegungsspezifikation haben.
- Erfahren Sie mehr über diesen Prozess in unserem Artikel zur Installation von Magnetspulenventilen.
- Verkabelung des Magnetspulenventils am Druckschalter:
- Verbinden Sie einen Draht vom Magnetspulen-Entlastungsventil mit der Lastseite des Druckschalters. Dies ist normalerweise in der Verdrahtungsdiagramm des Druckschalters angegeben.
- Der andere Draht vom Magnetspulen sollte an einem Neutral- oder Massepunkt angeschlossen werden, abhängig von den Anforderungen des Magnetspulenventils.
- Überprüfen der Motoranschlüsse des Kompressors: Stellen Sie sicher, dass der Kompressormotor korrekt mit dem Druckschalter verkabelt ist. Der Motor sollte starten, wenn der Luftdruck unter die Niederdruckeinstellung des Schalters fällt, und stoppen, wenn er die Hochdruckeinstellung erreicht.
Lösung häufiger Probleme
Eine Fehlfunktion eines Luftkompressor-Entlastungsventils kann zu Undichtigkeiten führen, wenn es nicht ordnungsgemäß schließt, und sogar dazu führen, dass der Kompressormotor nicht startet, wenn das Ventil nicht richtig öffnet. Die Ursachen und Lösungen für diese häufigen Probleme sind unten aufgeführt:
- Schmutz im Ventil: Manchmal verunreinigen externe Einflüsse (Staub, Teflon usw.) das Innere der Magnetspulenventile und verursachen eine Gerätemalfunction. Um zu bestätigen, dass dies die Ursache des Problems ist, zerlegen Sie das Ventil, inspizieren Sie den internen Zustand, führen Sie bei Bedarf eine geeignete Reinigung durch, installieren Sie das Magnetspulenventil erneut und testen Sie es, um die Leistung zu überprüfen. Es wird auch empfohlen, die Vorgängerleitungen des Luftkompressor-Entlastungsventils zu überprüfen. Der Schmutz könnte aus einem anderen Punkt im System stammen, und die interne Reinigung des Ventils könnte eine vorübergehende Lösung sein, aber das Problem würde erneut auftreten.
- Beschädigte interne Komponenten: Während der internen Inspektion eines Magnetspulenventils müssen alle beschädigten Teile (Membran, Dichtungen oder O-Ringe) ersetzt werden.
- Elektrische Probleme: Bestätigen Sie, dass Spannung und Frequenz korrekt sind. Überprüfen Sie den Zustand der Spule und messen Sie ihren Widerstand. Wenn er gegen Null tendiert, ist diese Spule verbrannt und muss ausgetauscht werden. Lesen Sie unseren technischen Artikel über wie man eine Magnetspulenventilspule ersetzt für weitere Informationen.
- Position des Ventils: Stellen Sie sicher, dass das Ventil mit dem Luftstrom in der richtigen Ausrichtung installiert ist, indem Sie auf die Pfeilanzeige am Ventilgehäuse achten.
FAQ
Was macht das Entlastungsventil an einem Luftkompressor?
Dieses Gerät wird von Luftkompressoren verwendet, um die eingeschlossene Luft in der Kompressionskammer freizusetzen, wenn der Tankdruck seinen maximal voreingestellten Wert erreicht.
Braucht ein Luftkompressor ein Entlastungsventil?
Ja, ein Luftkompressor benötigt ein Entlastungsventil. Das Ablassen der Luft durch das Entlastungsventil ist entscheidend, damit der Kompressormotor ohne jeglichen Aufwand wieder starten kann.