Drucküberwachung in Pumpsystemen
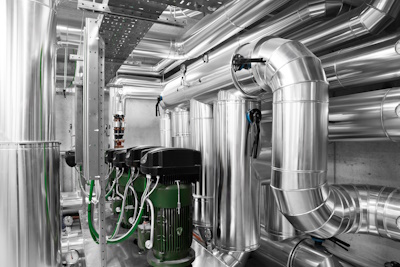
Abbildung 1: Drucküberwachungsgeräte gewährleisten einen effizienten und sicheren Betrieb in HLK-Systemen
Die Überwachung des Drucks in Pumpsystemen ist für die Aufrechterhaltung einer optimalen Leistung und die Identifizierung potenzieller Probleme unerlässlich. Abweichungen von den Standarddruckniveaus können auf Probleme wie verstopfte Filter, blockierte Rohre oder abgenutzte Laufräder hinweisen. Durch die konsequente Verfolgung von Druckdaten können Wartungsteams diese Probleme frühzeitig erkennen und Korrekturmaßnahmen ergreifen, um weitere Schäden zu verhindern und einen effizienten Pumpenbetrieb zu gewährleisten. Dieser Artikel untersucht, wie die Aufrechterhaltung eines optimalen Pumpendrucks die Effizienz und Zuverlässigkeit von Pumpsystemen verbessert.
Inhaltsverzeichnis
- Bedeutung der Drucküberwachung in Pumpsystemen
- Hauptkomponenten eines typischen Pumpsystems
- Arten von Drucküberwachungsgeräten in einem Pumpsystem
- Unabhängige und voneinander abhängige Geräte
- Anwendungen von Drucküberwachungsgeräten in der Pumpenindustrie
- FAQs
Sehen Sie sich unsere Online-Auswahl an Drucküberwachungsgeräten an!
Bedeutung der Drucküberwachung in Pumpsystemen
Pumpen werden in verschiedenen Systemen wie Luftkompressoren, Bewässerungssystemen und Wärmetauschern eingesetzt, um Luft oder Wasser zu bewegen. Wenn der Druck in diesen Systemen zu hoch oder zu niedrig ist, kann dies schwerwiegende Folgen für die Pumpe, die Rohre oder das gesamte System haben. Die meisten Ingenieure wählen Pumpen, die innerhalb von 80-110% ihres Best Efficiency Point (BEP) arbeiten, wo die Pumpe am effizientesten ist. Der Betrieb außerhalb dieses Bereichs kann die Pumpenleistung beeinträchtigen, weshalb die Drucküberwachung für die Maximierung der Effizienz von entscheidender Bedeutung ist.
Unzureichender Druck kann sich auf verschiedene Weise negativ auf die Leistung eines Pumpsystems auswirken:
- Erhöhter Energieverbrauch: Pumpen, die mit niedrigerem Druck arbeiten, benötigen oft mehr Energie, um die gewünschten Durchflussraten zu erreichen. Durch die Überwachung des Drucks können die Pumpeneinstellungen optimiert werden, um den Energieverbrauch zu reduzieren und die Effizienz zu steigern.
- Geringere Durchflussrate: Bei unzureichendem Druck sinkt die Durchflussrate, was dazu führen kann, dass die Pumpe die Systemanforderungen nicht erfüllt. Dies kann zu Ineffizienzen in industriellen Prozessen oder zu Engpässen in der Wasserversorgung führen.
- Verkürzte Lebensdauer der Komponenten: Niedriger Druck belastet die Pumpenkomponenten zusätzlich und führt zu einem schnelleren Verschleiß. Lager, Dichtungen und Laufräder sind unter diesen Bedingungen besonders anfällig für Beschädigungen, was die Gesamtlebensdauer des Pumpsystems verkürzen kann.
Hauptkomponenten eines typischen Pumpsystems
Ein typisches Pumpsystem umfasst mehrere wesentliche Komponenten, die die Flüssigkeitsbewegung erleichtern:
- Pumpe: Die Pumpe befördert verschiedene Flüssigkeiten durch mechanische Einwirkung von einem Ort zum anderen.
- Motor oder Antrieb: Die Energiequelle, die die mechanischen Komponenten der Pumpe antreibt und Energie in kinetische Energie für die Flüssigkeitsbewegung umwandelt.
- Rohrleitungen und Ventile: Ventile und Rohrleitungen in einem Pumpsystem (Abbildung 6) steuern den Fluss und die Richtung von Flüssigkeiten und gewährleisten einen effizienten und sicheren Transport von einem Ort zum anderen.
- Steuerungssysteme: Geräte und Systeme, die den Betrieb der Pumpe regulieren, wie Drehzahlregler, Durchflussmesser, Druckregelventile und Überwachungsgeräte.
- Kupplungen und Lager: Kupplungen und Lager in einem Pumpsystem verbinden und richten rotierende Komponenten aus und minimieren gleichzeitig Reibung und Verschleiß, um einen reibungslosen und effizienten Betrieb zu gewährleisten.
Arten von Drucküberwachungsgeräten in einem Pumpsystem
Manometer
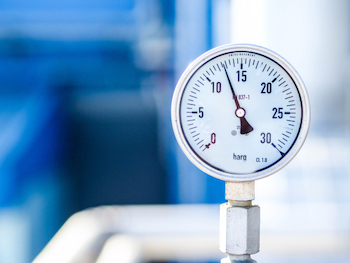
Abbildung 2: Manometer
Manometer werden typischerweise in der Nähe der Pumpe oder am Drucktank installiert. Sie messen und zeigen den Flüssigkeitsdruck an und stellen sicher, dass das System innerhalb sicherer Parameter arbeitet. Zum Beispiel überwacht ein Manometer für eine Wasserpumpe oder Brunnenpumpe den Wasserdruck, um die gewünschten Niveaus aufrechtzuerhalten, Probleme zu diagnostizieren und den Pumpenbetrieb zu steuern. Es wird in der Regel über einen Gewindeanschluss angeschlossen und mit Steuergeräten wie Druckschaltern integriert, um die Systemleistung zu automatisieren und zu optimieren. Lesen Sie unseren Artikel Manometer-Übersicht für weitere Informationen über die Funktionsweise und Anwendungen von Manometern.
Drucksensor/Druckmessumformer
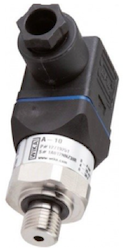
Abbildung 3: Druckmessumformer
Drucksensoren oder Druckmessumformer (Abbildung 6 mit F gekennzeichnet) werden an kritischen Punkten im System installiert, wie z.B. in der Nähe der Pumpe oder entlang der Rohrleitung. Sie wandeln den Eingangsdruck in proportionale elektrische Signale zur Überwachung und Steuerung um. In Pumpsystemen liefern sie präzise und kontinuierliche Druckdaten, die für die Echtzeitüberwachung, Automatisierung und Sicherheitsmechanismen verwendet werden können. Diese Sensoren sind in Steuerungssysteme integriert, um den Pumpenbetrieb anzupassen, Alarme auszulösen oder das System bei abnormalen Druckbedingungen abzuschalten. Lesen Sie unseren Artikel Druckmessumformer-Übersicht für weitere Informationen über die Funktionsweise und Arten von Druckmessumformern.
Druckschalter
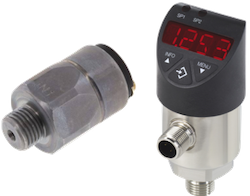
Abbildung 4: Druckschalter
Druckschalter (Abbildung 6 mit M gekennzeichnet) werden typischerweise in der Nähe der Pumpe oder des Drucktanks installiert. Sie überwachen den Druck innerhalb des Systems und aktivieren oder deaktivieren elektrische Stromkreise basierend auf voreingestellten Druckschwellen. Ein Druckschalter für eine Pumpe automatisiert den Pumpenbetrieb. Wenn beispielsweise der Systemdruck unter einen bestimmten Wert fällt, schließt der Druckschalter seine Kontakte, um die Pumpe einzuschalten, und wenn der Druck den oberen Schwellenwert erreicht, öffnet er die Kontakte, um die Pumpe auszuschalten. Dies gewährleistet konstante Druckniveaus, verhindert ein Überlaufen der Pumpe und schützt das System vor Schäden durch Über- oder Unterdruck. Lesen Sie unseren Artikel Druckschalter-Übersicht für weitere Informationen über die Funktionsweise von Druckschaltertypen, ihre typischen Auswahlkriterien und ihre Anwendungen.
Druckregelventil
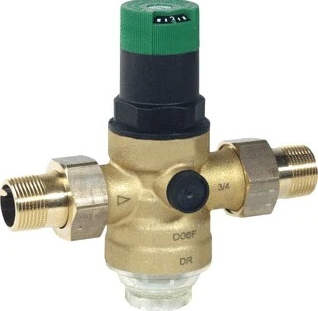
Abbildung 5: Wasserdruckregler
Druckregelventile werden typischerweise nach der Pumpe installiert. Sie halten einen konstanten Ausgangsdruck aufrecht, unabhängig von Schwankungen des Eingangsdrucks oder der Durchflussnachfrage. Zum Beispiel stellt eine Kraftstoffpumpe mit einem Druckregelventil sicher, dass der Kraftstoff mit einem konstanten und optimalen Druck an den Motor geliefert wird. Dies gleicht alle Schwankungen in der Kraftstoffversorgung aus und hilft, Probleme wie Kraftstoffmangel, Überdruckbildung und mögliche Schäden an den Kraftstoffeinspritzern oder anderen Motorkomponenten zu verhindern. Lesen Sie unseren Artikel Druckregelventil-Übersicht für weitere Informationen über die Bauform und Funktionsprinzipien von Druckregelventilen.
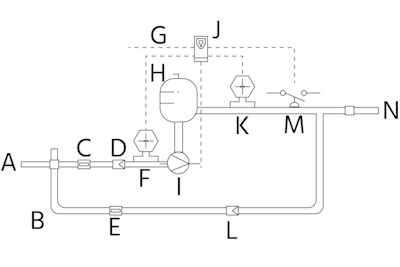
Abbildung 6: Beispiel eines Wasserpumpsystems: Wasserversorgung (A), optionaler Bypass (B), Kugelhahn (C, E), Rückschlagventil (D, L), Drucksensor (F, K), Stromversorgung (G), Drucktank (H), Pumpe (I), Frequenzumrichter (J), Druckschalter (M) und Durchflussausgang (N).
Unabhängige und voneinander abhängige Geräte
Während die meisten Drucküberwachungsgeräte so konzipiert sind, dass sie zusammenarbeiten, können einige unabhängig funktionieren:
-
Unabhängige Geräte:
- Manometer: Manometer können unabhängig arbeiten und manuelle Druckmessungen liefern, ohne dass eine Integration mit anderen Systemen erforderlich ist.
- Druckregelventile: Druckregelventile können einen konstanten Ausgangsdruck aufrechterhalten, ohne dass Eingaben von anderen Überwachungsgeräten erforderlich sind.
-
Voneinander abhängige Geräte:
- Drucksensoren/Druckmessumformer und Steuerungssysteme: Diese Geräte sind für die Echtzeitüberwachung und -steuerung aufeinander angewiesen. Der Sensor liefert Daten, und das Steuerungssystem verwendet diese Daten, um den Pumpenbetrieb anzupassen.
- Druckschalter und Pumpen: Druckschalter sind oft direkt mit Pumpen verbunden und automatisieren deren Betrieb basierend auf den Druckniveaus.
Anwendungen von Drucküberwachungsgeräten in der Pumpenindustrie
- Wasserhebeanlagen: Pumpen werden verwendet, um Wasser auf höhere Ebenen zu heben, wo herkömmliche schwerkraftbetriebene Systeme nicht ausreichen. Drucküberwachungsgeräte gewährleisten den Standardbetrieb und halten optimale Druckniveaus aufrecht.
- Reinwassersysteme: In Reinwassersystemen transportieren Pumpen Wasser über Rohrleitungen zwischen Aufbereitungsanlagen. Druckinstrumente liefern Rückmeldungen an Frequenzumrichter (VFDs) für einen zuverlässigen Transport und eine konstante Druckaufrechterhaltung.
- Abwasserpumpsysteme: Pumpen befördern Abwasser zu Kläranlagen. Die Überwachung des Eingangs- und Ausgangsdrucks hilft bei der Kontrolle der Durchflussraten und stellt sicher, dass das System innerhalb sicherer Druckgrenzen arbeitet.
- Industrielle Pumpsysteme: Diese werden in der chemischen Verarbeitung, der Öl- und Gasindustrie und der Fertigung eingesetzt und sind auf Drucküberwachung für Sicherheit und Effizienz angewiesen. Kontinuierliche Daten und Echtzeitrückmeldungen helfen dabei, die gewünschten Druckniveaus aufrechtzuerhalten und bei Bedarf Alarme auszulösen.
- HLK-Systeme: Pumpen zirkulieren Wasser oder Kältemittel in HLK-Systemen. Drucküberwachungsgeräte gewährleisten einen effizienten und sicheren Betrieb, liefern Steuerungsrückmeldungen und erleichtern Wartungsprüfungen.
- Brandbekämpfungssysteme: Pumpen liefern in Notfällen Wasser oder Feuerlöschmittel. Druckgeräte stellen die Systemaktivierung und die ordnungsgemäße Druckabgabe sicher, zeigen die Systembereitschaft an und halten den Druck aufrecht.
Beispiel
Betrachten wir ein kommunales Wasserversorgungssystem, das einen konstanten Druck aufrechterhält, was für eine zuverlässige Wasserversorgung der Verbraucher entscheidend ist. Drucksensoren überwachen den Druck an verschiedenen Punkten im Verteilungsnetz. Die Daten dieser Sensoren werden an ein zentrales Steuerungssystem weitergeleitet, das Frequenzumrichter zur Anpassung der Pumpendrehzahlen verwendet. An kritischen Punkten sind Druckschalter installiert, die automatisch Reservepumpen aktivieren, wenn der Druck unter einen bestimmten Schwellenwert fällt. Druckregelventile sorgen dafür, dass der Ausgangsdruck stabil bleibt und Schwankungen verhindert werden, die die Wasserversorgung stören könnten.
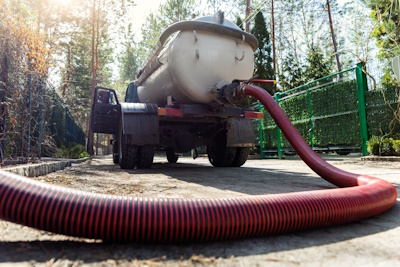
Abbildung 7: Abwasserpumpsysteme verwenden Drucküberwachungsgeräte, um die Durchflussraten zu steuern und sicherzustellen, dass das System innerhalb sicherer Druckgrenzen arbeitet.
FAQs
Was ist ein Druckschalter für eine Brunnenpumpe?
Er stellt sicher, dass der Wasserdruck innerhalb des gewünschten Bereichs gehalten wird, indem er die Pumpe automatisch steuert, um eine konstante Wasserversorgung zu gewährleisten und das System vor Schäden zu schützen.
Warum ist ein Pumpendrucktest erforderlich?
Ein Pumpendrucktest diagnostiziert und verhindert potenzielle Probleme in Pumpsystemen. Der Test misst den Druck an verschiedenen Punkten im System, um sicherzustellen, dass es ordnungsgemäß funktioniert.